Document Type
Book Chapter
Files
Download Full Text (7.4 MB)
Date
5-27-1955
Keywords
Henry Edris, barn raising, carpentry, lumber, Pennsylvania Dutch dialect, farms
Description
Handwritten manuscript entitled, "Raising the Barn", compiled by Victor C. Dieffenbach, dated May 27, 1955. Within, Dieffenbach describes how Pennsylvania barns are raised. He details the people, parts and tools involved, and the entire process from start to finish.
Corresponds to:
577-215-1 through 577-215-12
Transcription
Raising the Barn.
Die Shire Uff-schtella udder Uff-schlawga.
I can well remember a lovely Summer morning years ago, when Dad announced at the breakfast table: “Heidt gaina meer un helfa em Hanner Aider sei shire uff-schtella! Do gaisht awe mitt,” he said, looking at me. (Today we'll go help Henry Edris put up his barn.) “Ya, un Ich gay awe mitt”, said a gruff voice from the upper end of the table. That was Grandad, a veteran – a lifelong builder of houses, barns, bridges, school-houses and several big churches. ‘Ich con ols nuch mainer do os we en lot yunga kenna,” he proudly announced; and how right he was. He was then eighty years old.
So we set out on foot, as it was no more than a mile to our neighbor’s farm. Arrived on the site of the new barn the old man was warmly greeted by numerous friends, as well as by the boss-carpenter who built the barn, viz. Elias Gearhardt of Jonestown, Pa., a building contractor of repute, a good and reliable man, and a good mechanic. Altho also well advanced in years, still he was not as old as my grand-sire. So, as to show the respect he owed Granddad for his years, as well as for his experience and expert knowledge of the craft, the contractor asked my Grandad to take over, or to supervise the job. He refused; he said that the craftsmen were new and strange to him – that Gearhardt might have ways and signs peculiar to an individual boss and he did not want – in fact he would not accept the responsibility of such an intricate undertaking.
”But I’ll help,” he said – “I’ll show the men which piece to carry in, and where to put the lumber, and you can supervise the erection of the building!” So said – so done.
Now, when carpenters get ready to build a new barn (not to erect it) the very first requisite is good lumber, suitable for framing it. This is either cut at a nearby sawmill, or it is bought on the open market. The contractor has a list of all the lumber required – “en holtz-bill,” on it is listed the exact dimension of each piece, viz. the length, width, and the height, and the number of each. All pieces are a trifle longer than actually needed, since all have to be squared at each end.
Once the lumber is at the building-site, then the barn has to be framed, i.e. each individual piece is cut in exact length; all the mortises and tenons are marked and cut. The material for each bent (“die wondt”) is marked with a chisel in Roman numerals. Corner-post no .1. for end-wall has a cut on it like this I, close to tenon and a similar I close to the corresponding mortise. Each bent is fitted and put together out on the landing; once it fits accurately, it is taken apart and piled up separately. The second one is marked II and so on to the other end of the barn. One barn that I helped to raise years ago, the carpenter had used lumber crayons to mark the various parts. By the time the “big day” arrived, nearly all the marks had disappeared from the sun and rain, the parts had not been accurately fitted – nobody seemed to know where anything should go, and it was a mess. Finally one old timer yelled – “Doe iss en tsopp a owver ’s iss ken loch doe fer en nei do – wos doot mer?” He meant he had a post with a tenon and no mortise or hole to put it in. And a rowdy in the crowd yelled “Dunnerwetter – goy hame tzu der Mem!” Thunderation – go home to Mom!
First of all are carried in the posts – the big square ones, that go into the basement, and support the middle of the super-structure; they are put on end, upright underneath the bent, that will later be placed in position. The center row of these posts, going lengthwise thru the barn are 18 inches shorter than the rest, and support the monstrous main girder – “der darrich-tsook.” On top of this “big-stick” are laid the beams (“die bolka”) and then the floor.
This big timber may be in one piece, or it may be spliced, and held together by a wooden key. See Fig 1. I saw one such girder, 18 inches square, 70 feet long, in one solid piece, and not one sliver of bark showing on a corner. Liever Gott – wos fer en baum waur sell?
Once the big girder is placed in position – its end firmly imbedded in solid masonry, then the big sills (“die schwella”) are put on the stone foundation all around; they are fitted together at each corner, as we Pa. Dutch say --:”tsumma-geblawd” i.e. one-half of the thickness and the entire width of the sill measuring from the corner is cut out; then a mortise is made through both pieces and the corner-post has a tenon going down thru the two sills, keeping them from spreading apart. The four corner-posts are thus anchored, one might say, to the foundation, thus binding the entire building together. Hence the tenon on the corner-post is called --:”der binn-tsoppa – i.e. the binding pin or peg. Next come the beams – “die bolka”) laid cross-wise on top of sills and the girder; and on top of these is laid the floor.
Bank-barns – (“die Schweitzer shire”) so called from their barns in Switzerland, by the Swiss and Palatinate pioneers, usually have a fore-bay (“der fore-bau – der fore-bauer, or der fore-schuss”) This is done by having the end walls of the barn six feet wider than the width of the basement. Piers of masonry are put up between door and window openings, and on these piers is laid a stick of wood, flush with the top-edge of the big girder. This is called – (“die mauer-lott”) So, you see, the super-structure is six feet wider than the basement, and that gives your “der fore-bau” or fore-bay.
Now the floor is laid (oft-times just temporarily) so the workmen have something to stand on while erecting the framework. Now a group of men goes out to the pile marked no.1, each couple (they are always paired-off as to size) carry a short round stick of wood, from four to five foot long, two inches thick, preferably hickory or ash. These are used to carry in the lumber. (“Des sin die houd-hevvel, fer des lumber nei drawga.”) All the lumber from pile no.1 is carried in, one piece at a time, and all laid on the floor, each piece in its proper place —each mortise at its corresponding tenon in the sill, and the tops of the posts facing inwards, or towards the center. The entire bent (die wond) is now put together, and wooden pegs driven into previously-bored holes, so all mortises and tenons are locked tight.
Now get your pikes! (“Now grickt oll ire schtoch-aiter, or schticher!”) These are long round poles of tough wood, about 12 foot long, two inches thick, smooth, and have an iron pin in the middle of one end, quite sharp. A dozen men lift up the bent at the innermost side, and others slide big blocks of wood under it. All now lift it up as high as they can. Some tie a couple of ropes to the top of the bent, to keep it from going over once it is perpendicular. All once more get a good grip, the pikers get a good toe-hold and now - : “Up-up-up she goes!” All push - the men at the holes each hold a crowbar or digging iron, so as to guide the tenon into its hole. The ropers now guide it, a few boards are nailed to the sill with one end, and all look to the master-carpenter standing on the top of a pile of logs, straddle-legged - a plumb-bob held between thumb and index-finger of the left hand. With the right hand he waves to the man at the corner-post – his hammer poised in mid-air.
”In-in-easy-easy-holdt—sell waur tsu feel – bring en witter rous –easy – now nuch em bissel – mainer – nuch en arsch-hore – holdt – Grawd recht—Schlawg en nei!” The man nails the brace-board at the corner-post, the post stands as solid as the pyramids and will continue to do so for a century or more.
Just a short time ago I scrutinized some of Grandad’s work—the very first barn he put up, about 120 years ago, and still in very good condition as regards the general construction. While the first bent was being raised a gang of men brought in pile no.2. and laid it in position, and the operation is repeated, bent by bent until the entire framework has been erected. If the framing or laying-out was skillfully and accurately done, necessitating no changes while setting it up, the work progresses very rapidly. I am sure that there were over 100 men on the job at the Edris barn. When the entire framework was up, Grandad relinquished his job to the carpenter-boss.
Now up with the roof-trees! (“Now nuff mitt da doch-schteel!”)
These are mortised into the plates – (“die schpann-petta”) on an angle, and slant outwards when in position, so that the weight of the purlines (“die dach-roota”) resting on the rooftree, and the roof proper, of whatever construction it may be, all press down, and the roof-tree, being strongly braced, keeps firm and solid.
Well, someone grabbed a roof-tree - a piece of timber "6x6" and about 8 foot long and carried it over and laid it on the barn floor. Somebody with a block and tackle hoisted it up, and another man at the top took it and carried it to its proper place. That is when we heard a yell, a crash, and then more yells, screams, curses, etc. Looking up we saw one of the apprentice carpenters – a young man who never in his life had been higher up than his Dad’s “uvverden”, when the hired-girl – (“die maud”) went up to hunt eggs, lying on his belly and holding on to the top of the bent with all six legs. That is what it looked like to him. He had dropped the roof-tree and it crashed down onto the barn floor, narrowly missing several men engaged in putting in the side wall (“die den-wond”)
The poor fellow was trembling so the entire structure was shaking. Everything was at a stand-still. Farmers, who had voluntarily helped and had done all they could so far were now nonplussed, for why should they go up if the carpenter could not take it. And right there is where the veteran builder came to the rescue; the stalwart octogenarian, still supple, and all six foot of him straight as a ramrod, grabbed a roof-tree, swung it on his shoulder and calling over his shoulder “Vic, come on – let's go,” he started out to the outermost hole. He went out on that plate like an acrobat, and I followed him with mine. Someone realized what we were doing to the morale of the party and followed suit.
The carpenter-boss got his man down – they almost had to hit him with a club so he would let go. The boss had a car – all this occurred some fifty years ago – so he took him to another farm where they were building a corn-brib, put him to work there, and then came back. He had some really good men and they put up the purlines and a few rafters and lunch was ready. This was served on long tables, out in the yard, under the trees. Neighboring farmers’ wives and girls, relatives and friends helped to prepare the meal and wait on the tables. Plenty of good food in the proverbial Pa. Dutch style, viz. ”helf der schwert, un fress bis do nimmy schlucka consht.” Everybody was happy and many were the compliments showered on the “old man” and - : (“seller schlick yung”) one old sister said—they belonged to the Church of the Brethren. I could have hugged her for that, only she seemed to be a bit along in years. But I am not yet sure if it wasn’t her daughter or niece or who, that I met at some social gathering, at a later date.
After dinner most of the farmers went home; some stayed and helped to carry in the rafters. The carpenters put them up, and old Henry told me on the sly “see gaina dort druvva rum we kotza, usht mer saint ken schwentz.”
On another farm, also not far away, someone neglected to put anything under the big girder, so it lay flat on the ground. Several tried to lift it up, so the rest could get the carrying poles under it. But they could get no grip on it or it was too heavy. When nobody seemed to be able to budge it, a short squatty farmer – Geo. Schucker, stood at the end of the log. He straddled it, stooped, dug his fingers in underneath, and presto – up it came, up to his knees above the ground.
“Schteckt en drunner,” I cried. Someone did, and we all got ours under and carried it in.
When Grandad, while in his hey-day of his building career built a monstrous barn for Titus Rauk, Prop. of the Buck Hotel, Jonestown. When I was knee-high to a bed-bug, the hotel man came out the farm on the day of the barn-raising and had a ten-gallon keg of whiskey for the men. Grandad lifted it out of the buckboard, put it in the spring-house, locked the door, and put the key in his pocket. Rauk said that he brought it out for the men.
Grandad said “Ya, un see greega in awe; usht net bis de shire uff iss. No kenna see soufa. My mann kenna no die schporra neff do, un won die onnera awe gsuffa sin.” And they did. He was a hard-working, hard-drinking man – clean – no driver, and had one of the best of gangs that ever pushed a saw or a plane.
Several years ago I helped to erect a barn that had been framed by a single carpenter, ably assisted by the farmer and his son, the regular hired man and a few hired by the carpenter, but no real mechanics. That barn went up like a cat up a pole—everything a perfect fit, from start to finish.
Years ago I helped where an old carpenter, who was steadily employed, was in charge of the construction. In the course of erecting it, one entire wall or bent had to be re-framed – i.e. made over, needlessly holding up half a hundred men. The writer can truthfully say that he helped in the erection of at least a dozen barns and several houses, not including several barns and a house of his own construction. And I still don’t claim to know it all; for what does one learn in 73 years? The time a man gets a slight understanding of Life’s values, and thinks he’s got a grasp of things, then he usually turns up his toes. And once in a while I even meet up with fellows my senior who tell me they never in their life helped to erect a barn or any other building. And so it goes.
May 27 - '55
Victor C. Dieffenbach
Language
English and Pennsylvania German
Rights Statement
This item is available courtesy of the Ursinus College Library Special Collections Department. It is not to be copied or distributed for commercial use. For permissions which fall outside of educational use, please contact the Special Collections Department.
Recommended Citation
Dieffenbach, Victor C., "Raising the Barn, May 27, 1955" (1955). Alfred L. Shoemaker Folk Cultural Documents. 233.
https://digitalcommons.ursinus.edu/shoemaker_documents/233
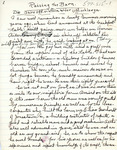
Included in
American Material Culture Commons, Cultural History Commons, Folklore Commons, Linguistic Anthropology Commons, Social History Commons, United States History Commons
Rights Statement
In Copyright. URI: http://rightsstatements.org/vocab/InC/1.0/
This Item is protected by copyright and/or related rights. You are free to use this Item in any way that is permitted by the copyright and related rights legislation that applies to your use. For other uses you need to obtain permission from the rights-holder(s).